Solutions
-
- Drilling Tools T38 3660Mm MM
Drilling Tools T38 3660Mm MM MF Thread...
-
- Hex22 Pneumatic Rock Drilling Tool
Small Hole Drillig Tools Hex22 7/11/12 Degrees Tools Taper Drill Rod...
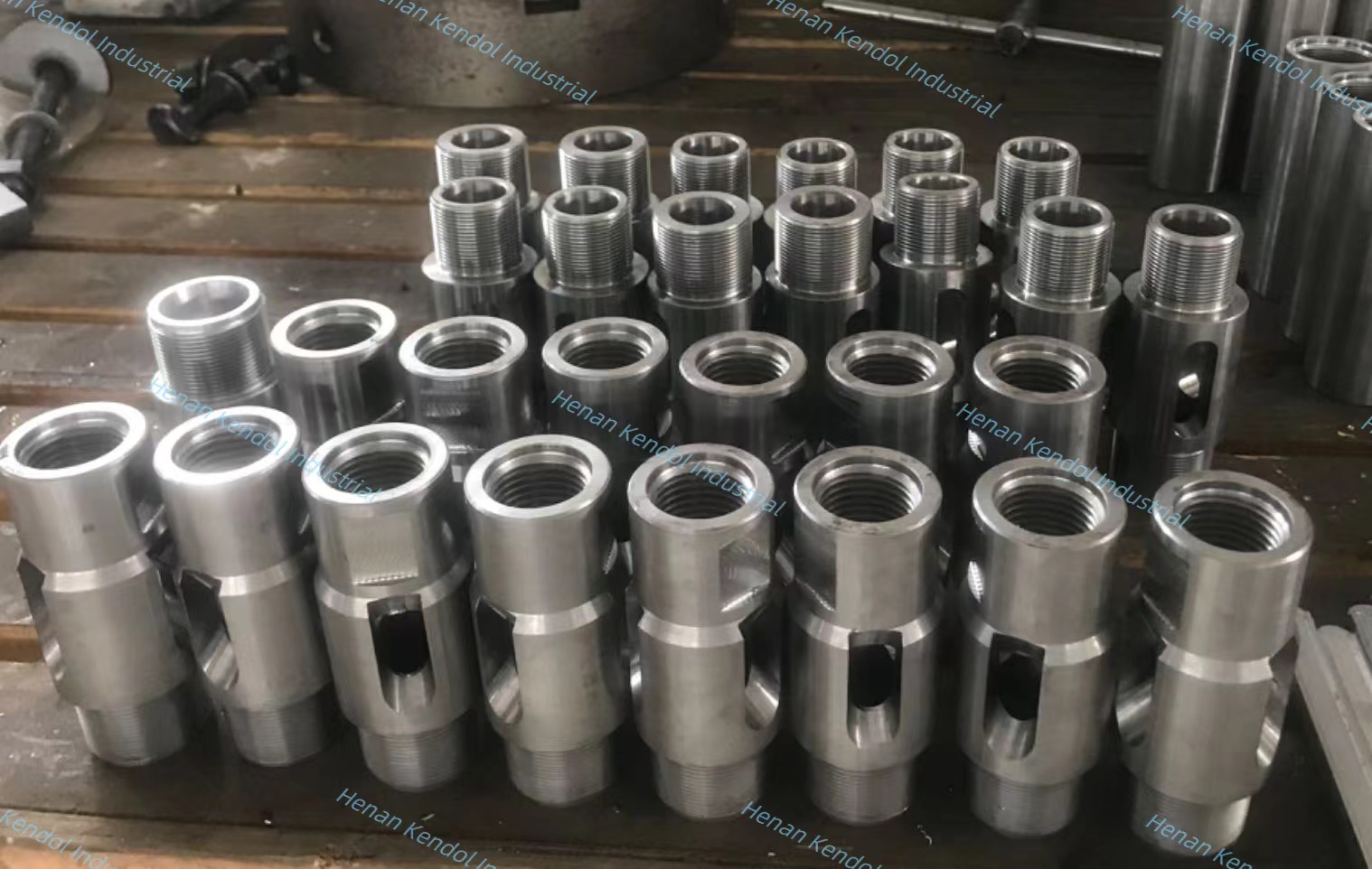
Sucker Rod Anti-Corrosion Coupling
Product Introduction
The sucker rod anti-corrosion coupling is a sucker rod anti-eccentric wear tool newly developed by our company. It has the characteristics of simple structure, easy use, long service life and relatively low cost. It is suitable for pumping wells with eccentric wear, especially for pumping wells and directional inclined wells with eccentric wear above the neutral point of the sucker rod. Below the neutral point of the sucker rod, it cooperates with the nylon centralizer on the sucker rod body to achieve better anti-eccentric wear effect.
Main Structure and Characteristics
- The technical core of this coupling:
Ni65A alloy powder is coated on the surface of the sucker rod coupling using a special surface treatment process to obtain a wear-resistant, corrosion-resistant and low friction coefficient coating. Its thickness is greater than 0.25mm, and its wear resistance is more than 10 times that of ordinary couplings. Reduce oil pipe wear by approximately 3 times.
- Has significant self-protective effect:
Ni65A alloy powder coating ensures that the coupling maintains excellent wear resistance and corrosion resistance in complex underground working conditions. The composition, structure, and hardness of the coating are very different from those of the oil pipe, which prevents and delays the initial occurrence of adhesive wear. The high hardness of the coating enhances the coupling’s resistance to abrasive wear.
- It has a good protective effect on oil pipes:
The unique anti-wear element (e phase) in the Ni65A alloy powder coating is evenly transferred and attached to the surface of the oil pipe in the form of flakes during the friction process between the coating and the oil pipe, forming solid lubrication, protecting and slowing down the wear of the oil pipe surface. At the same time reduce
It reduces the friction coefficient between the coupling and the oil pipe and plays a role in reducing friction.
The Main Technical Parameters
Specification | Length
(m m) |
OD(mm) | Wrench square distance *longest(mm) | Matrix hardness HB | Coating hardness HV200 | Matrix material | coating material |
3/4″ | 101.6 | 41.3 | 38.1*31.8 | 200~240 | ≥595 | 40Cr | Ni65A Alloy powder |
7/8″ | 101.6 | 46 | 41.3*31.8 | 200~240 | ≥595 | 40Cr | Ni65A Alloy powder |
1″ | 101.6 | 55.6 | 47.6*31.8 | 200~240 | ≥595 | 40Cr | Ni65A Alloy powder |
Inquiry
Here you can submit any questions and we will get back to you as soon as possible. We will not disclose the information you submit to anyone, please rest assured.
Inquiry